

もっとも基本的な機械要素である『ねじ』。
そのねじに対する航空・宇宙産業のニーズから開発に成功した特許技術を、当社では日本・米国合わせて数多く保有しています。
その特許技術が多くの産業界にお役に立てることを確信し、この度当社では、知的資産の特許等をライセンス販売致します。
貴社の製品の機能向上、技術問題点の解決、新製品の開発に、お役立て下さい。

< 用途>
航空・宇宙産業、精密機械産業、製薬・食品産業、スポーツ・レジャー産業、半導体・化学製造
装置産業、自動車産業、電力・電機産業、上下水道・土木建築産業 等

本装置はプラズマ浸炭を主体とした多目的真空熱処理装置で、常用300℃~1,100℃で金属処理一般( 浸炭、窒化、浸炭窒化、焼入、焼戻、焼鈍、溶体化処理、時効処理、磁性処理、ろう付け)に使用できます。
(PCT:PlasmaCarburizingTreatment)
(GLC:Glass-likeCarbon)※GlassyCarbon
「プラズマ浸炭処理」は浸透拡散処理の一種で、真空中でプラズマを利用して硬化層を傾斜的に形成する表面改質硬化処理です。さらに当社では、チタンへのPCTを行うのと同時に、最表面にGLC( 硬質ガラス状炭素膜)を形成することに成功しました。「PCT+GLC」により、耐食性、耐摩耗性、潤滑性( 低摩擦係数)、離型性、ガス不透過性、生体親和性が向上し、チタン金属の工業上の利用価値を高め得る日本発の技術として世界中に発信していこうと考えています。
■PCT+GLC 概要図
チタン金属にPCTをすることで、硬いPCT層の上に、より硬いGLC層が形成されます
「プラズマ浸炭処理」は浸透拡散処理の一種で、真空中でプラズマを利用して硬化層を傾斜的に形成する表面改質硬化処理です。
さらに当社では、チタンへのPCTを行うのと同時に、最表面にGLC(硬質ガラス状炭素膜)を形成することに成功しました。
「PCT+GLC」により、耐食性、耐摩耗性、潤滑性(低摩耗係数)、離型性、ガス不透過性、生体親和性が向上し、チタン金属の工業上の利用価値を高め得 る日本発の技術として世界中に発信していこうと考えています。"Plasma-carburizing" is one of the plasma surface diffusion process in the vacuum and significantly improves wear resistance by producing high hardness layer.
We have developed that a GLC film formed on the carburized titanium surface at the same time.
Our newly combined surface modification technique are very effective for improvement of corrosion resistance, wear resistance, lubricity (low friction coefficient), releasability, gas impermeability and biocompatibility
■PCT+GLC後のラマンスペクトル
Raman spectrum pattern for GLC coated Plasma-carburized (PCT+GLC) titanium sample.
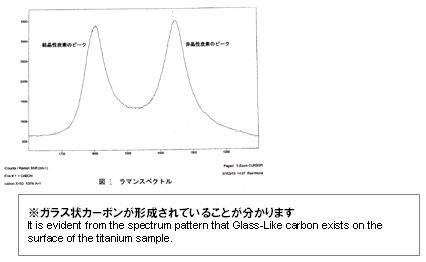
■PCT後の純チタン、チタン合金の硬度と硬化層データ
Depth profiles of Vickers hardness for plasma-carburized titanium and its alloy samples.
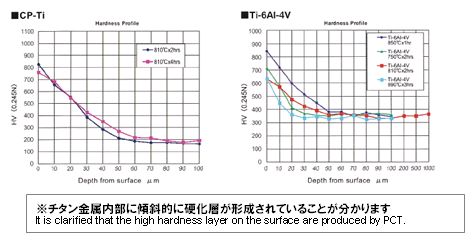
チタン基材電極での利用
Application to high-performance titanium electrodes.
チタン基材に導電性のPCT+GLCを被覆した「PCT+GLC電極」利用の取組みを行っています。
チタン金属は白金めっき等をすることで、今まで耐食性に優れた電極用金属材料として用途拡大を行ってきましたが、当社の特許技術により高性能な不溶性電極が開発されることを期待します。
We are developing new titanium insoluble electrodes introduced by using our patented process (PCT+GLC) .
硬化処理の後、ねじ転造が可能です
今後需要が拡大する燃料電池用のセパレーターへご利用下さい
【新製品情報】SDCプロテクトパーツ・カバーキャップ「Hシリーズ」
SDCプロテクトパーツ
カバーキャップ「Hシリーズ」が当社ラインナップに加わりました。
製品詳細・サンプルのご依頼等についてはお気軽にお問合せ下さい。
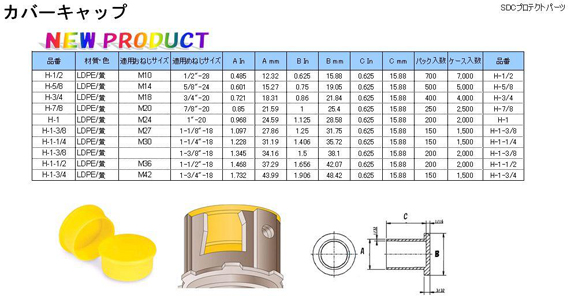
JISQ9100 認証取得
航空宇宙品質マネジメントシステム
JISQ9100 認証取得
株式会社田中(関連会社:株式会社エスディーシー)は2010年4月28日、航空宇宙産業における国際品質マネジメントシステム JIS Q 9100の認証を取得致しました。
認証取得の内容
1.認証規格
JISQ9100 : 2004
JISQ9001 : 2008(ISO9001 : 2008)
2.登録事業者
株式会社田中〔本社〕
(大阪市住吉区帝塚山中1-10-6)
関連組織
株式会社田中〔南大阪事業所〕
(大阪府南河内郡河南町加納657-5)
株式会社エスディーシー〔本社・工場〕
(大阪府堺市堺区神南辺町4丁132番地)
3.登録範囲
航空機及び宇宙機器用プラズマ表面硬化処理
および真空熱処理金属部品の製造
(Manufacture of Plasma Heat Treated or
Vacuum Heat Treated Aerospace Metal Parts)
4.登録日
2010年4月28日
5.認証機関
日本検査キューエイ株式会社(JICQA)
当社はJISQ9100の認証取得により、 航空宇宙分野でSDCプラズマ表面硬化処理の更なる拡販を目指します。また、これまでSDCボルトシリーズで培ってきた研究開発・品質保証を活かして、今後とも皆様のニーズに合う製品を提供していきたいと願っています。
*** JISQ9100航空宇宙品質マネジメントシステムとは・・・ ***
ISO 9001をベースとし、航空宇宙産業特有の要求事項を追加した航空宇宙品質マネジメントシステム(Aerospace Quality Management System,AS-QMS)であり、世界の航空宇宙産業各社により設立された国際航空宇宙品質グループ(IAQG:International Aerospace Quality Group)が制定した国際統一規格(IAQS9100)に基づき制定された日本工業規格です。
JISQ9100は、米国ではAS9100、ヨーロッパではEN9100として同じ内容でIAQCにて規格化され、相互承認されています。
SDCクリーンボルトシリーズ サイズ表
<製品仕様>
■材質:SUS316L
■表面処理:SDCプラズマ表面硬化処理
■オプション(特注品)
・真空用ガス抜き穴加工品
・精密洗浄+クリーンルーム用梱包(2重梱包)
●印・・・在庫完了サイズ
○印・・・対応可能サイズ
SDCクリーンボルト
SCB-CSF
形状:キャップスクリュー(六角穴付きボルト)
SCB-HBF
形状:六角ボルト(全ねじ)
SCB-HBH
形状:六角ボルト(半ねじ)
SDCクリーンナット
SCN-HN1
形状:六角ナット(1種)
*上記表以外の形状、寸法、規格外の寸法なども対応可能ですので
どうぞお気軽にお問合せ下さい。
20090507
配管技術 2008年9月増刊号『最新の特殊管材料』 2008年9月15日発行
クリーン環境用ステンレス鋼ボルト
潤滑剤を使用せずに焼付き・かじりを防止
1.はじめに
当社はステンレス鋼の焼付固着防止の問題を解決することにより、フランジ接合用にステンレス鋼製ボルト・ナット開発した草分け的存在であり、常に顧客の ニーズを基に研究開発を行ってきた。主な製品例は「SDCボルト」で知られる水道配管用のステンレス鋼製ボルト・ナットであり、「SDCボルト」はボル ト・ナット締付け時の焼付き防止効果ばかりでなく、締付け管理の際のトルク係数を安定させることによって適正な締付け結果を得られることが顧客のニーズに 適合し、1981年発売開始から27年経過した現在でも、全国の水道事業所などで使用されている。
その後、SDCボルトシリーズとして異種金属管接合時の電食(電池作用腐食)を防止する「SDC防食ボルト」、1000Vの電圧を絶縁する「SDC電流 絶縁ボルト」などがシリーズ化され、全国の水道事業所だけに留まらずプラントメーカーや各種機器でも使用されるに至っている。
1984年、米国のシアトルに現地法人SDC.US.CORPを立ち上げ営業活動を行った際に、世界最大の航空機メーカーであるボーイング社から、チタ ンの表面硬化処理技術の開発を求められた。この技術ニーズを基に技術開発を重ね、チタンへの表面処理の技術を開発、特許も取得した。
「SDCプラズマ表面硬化処理」はその後チタン製ボルト・ナットに適応され「SDCチタンボルト」、「SDCチタン合金ボルト」が生まれた。また、開発 した表面処理技術は「SDCプラズマ表面硬化処理技術」としてチタン部品の摺動箇所での磨耗防止対策処理として、航空宇宙部品や各種産業用ポンプや撹拌機 の磨耗防止や腕時計の外装部品やゴルフクラブの傷防止にも採用され、あらゆる分野にて威力を発揮している。
「SDCプラズマ表面硬化処理技術」はチタン材だけではなく、ステンレス鋼への表面硬化処理も可能にし、ステンレス鋼が粒界腐食により鋭敏化しない温度域で表面硬化処理ができる低温プラズマ表面硬化技術を確立した。
その後、ステンレス鋼製ボルトに「SDCプラズマ表面硬化処理」を施した「SDCクリーンボルト」(写真1)を開発し、無潤滑で乾燥式の焼付き防止ねじ として普及し始めている。本稿では、「SDCクリーンボルト」の特長や機械的性質など、プラズマ表面硬化処理技術の内容と共に紹介する。
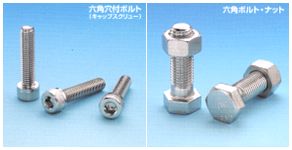
(写真1)
2.「SDCクリーンボルト」概要
配管ジョイントに用いられている軟鋼及び鋳鉄製のボルト・ナットは被締結物が健全であるにも関わらず、ボルトが異常腐食(電食)を起こすことが非常に問 題視されていた。そこで耐久性、耐食性に優れたステンレス鋼製への代替が着目され、現在ではめざましい普及をみるに至った。しかし、従来のステンレス鋼製 ボルト・ナットは締付けた時に焼付固着を起こすという問題が発生する。ステンレス鋼製ボルト・ナットの焼付く原因は主に下記3点の要因が考えられる。
①ステンレス鋼製は摩擦係数が大きく、従ってねじのかみ合い面での摺動抵抗が大きくなってしまう。
②ステンレス鋼は、熱伝導率が小さい(鋼の1/3)ためにねじのかみ合い面で発生した熱が発散されにくく、局部的に高温になり易い。
③ステンレス鋼は、熱膨張係数が大きい(普通鋼の約1.5倍)
これら3つの要因が相乗効果をきたし、ねじ部の膨張が大きくなり焼付きが起きやすくなる。
以上のような欠点を克服する防止策として、潤滑剤・めっきを使用せず、ステンレス鋼製ボルト・ナットの焼付きを防止するねじとして、「SDCプラズマ表面硬化処理」の適用により「SDCクリーンボルト」を開発した。
特に不純物を極力嫌う半導体製造装置用真空装置内部やクリーンルーム内、食品・飲料関係、化粧品・医療関係の配管部では、ボルト・ナットの締付け時に潤 滑剤やめっき・コーティングなどの焼付防止対策は使用できない。理由として、潤滑剤に関してはクリーンルーム内でコンタミとなって製品に悪影響を与え、 めっき・コーティングに至っては、締付け時のねじ部に高トルクがかかることからめっきが剥がれ落ち、潤滑剤を使用した時と同じ問題が起こる。また、温度が 上昇すると潤滑剤の蒸発、めっきの変質が起きてしまう。そのため、潤滑剤を使用しない焼付き防止の「SDCクリーンボルト」が必要不可欠である。
3.SDCプラズマ表面硬化処理
金属の表面硬化処理には、蒸着(PVD,CVD等)、塗装やめっきなど異種材料を表面にコーティングする処理と、表面から内部へ炭素や窒素原子を浸入拡 散させる浸透拡散処理がある。「SDCプラズマ表面硬化処理」は浸透拡散処理の一種で、真空中でプラズマを利用して硬化層を傾斜的に形成する表面を改質処 理する。(硬度データは図1に示す)
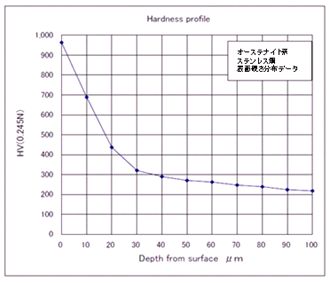
(第1図)
そのため、めっき・コーティングと異なり、剥離してコンタミが発生することが全くない。この処理技術はチタン・チタン合金及びステンレス鋼の耐食性を劣 化させずに硬化処理することが可能で、薬品・食品・飲料プラント、半導体製造装置、クリーンルーム内部など幅広く適用することができる。
また、世界15ヶ国が共同で開発を進めている国際宇宙ステーション(ISS)の日本担当実験モジュール「きぼう」が日本時間6月1日に米スペースシャト ル「ディスカバリー」によって打上げられたが、この「きぼう」内部にも当社の技術が搭載されている。「きぼう」内には温度調節をするために冷却水を流す配 管が必要であり、その配管内部の圧力を一定に保つためのアキュムレーター(蓄圧器)が取り付けられる。その組み立ての際にねじ部の締付けを繰り返すことに より焼付き現象が発生するが、それを防ぐ目的として「SDCプラズマ表面硬化処理」が採用され、宇宙開発事業に対して必要不可欠な重要な技術として実証さ れている。
「SDCプラズマ表面硬化処理装置」の設備は1996年に研究用として小型のプラズマ浸炭処理装置をはじめとして、1999年に大型炉を㈱エスディー シー堺工場(テクノフロンティア堺)に設備、その後新エネルギー・産業技術総合開発機構(NEDO)殿のご支援を頂き特許設備の「SDCプラズマ表面硬化 処理装置」を完成させた。
またこの技術は二酸化炭素などの排出ガスが殆どでないクリーンで環境に優しい処理方法として各方面から注目されている。
4.「SDCクリーンボルト」の特性
4-1 特長
・不純物を嫌いクリーン度が求められる環境での潤滑剤及びめっき・コーティングなどを使用せずに焼付き・かじりを防止したステンレス鋼製ボルトである。
・「SDCプラズマ表面硬化処理」によってねじ部の表面硬化を行い、焼付きを防止する。
・めっき・コーティングなど異種材料を表面蒸着するものではないので剥離の心配がない。(コンタミの原因にならない)
・繰り返し使用や高温においても傾斜的な硬化層が得られているために剥離の心配がない。
・母材と同程度の耐食性を維持する。
・真空装置で使用されるガス抜き穴仕様も製造可能で、精密洗浄、クリーンルーム用梱包にも対応可能である。
4-2 締付け試験
本製品の最大の特長である焼付き防止を含む締結特性を「SDCねじ性能試験機」(写真2)を使用した締付け試験により確認した。この試験機は国有特許で ある「弾・塑性域締結ねじ性能試験機」(考案者 東京工業大学 名誉教授 丸山一男工学博士)から量産実用化に弊社が改良し、開発した試験機である。「SDCねじ性能試験機」は、実際の作業環境に近い状 態で、ねじの締結特性を評価する試験機であり、ねじ部トルク・座面トルク・締付けトルクなど各トルクを検出することができ、塑性域締結でのねじの挙動も確 認できる試験機である。
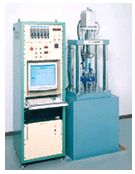
(写真2)
供試体として、六角穴付きボルト:M10×35を「SDCクリーンボルト」と無処理のものを用意し、ナットはステンレス鋼製六角ナットをセットし、ボルト回転による10回の繰返し締付けを行った。結果を図2に示す。
図中のねじ部トルクの線を確認すると、無処理は初回締付けは通常の値だが、締付け回数を重ねるうちに不安定になり、ねじ部に大きな変化が生じていることが 確認できる。8回目で焼付きが発生し、ねじが破壊した。「SDCクリーンボルト」は回数を重ねても安定した締付けが行われ、試験終了後も限界ねじゲージに よるねじ精度テストにも合格した。「SDCクリーンボルト」のねじ部は強固に強化されているのが確認できた。
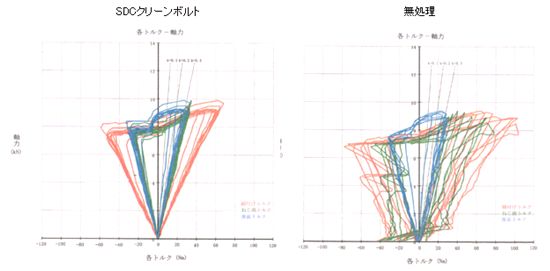
(第2図)
4-3 機械的性質
「SDCクリーンボルト」の機械的性質をJIS B 1054の「ステンレス鋼製耐食ねじ部品の機械的性質」の引張試験により確認した。供試体として、六角穴付きボルトM8×35を「SDCクリーンボルト」と一般品を用意し、比較検討した。結果を図3に示す。
両者の比較を分かりやすく表すため、表中では無処理のボルトの伸びを1mmオフセットしているが、引張強さは高く、伸びまた破断位置も同じであり、強度の低下は全くないことが確認できた。
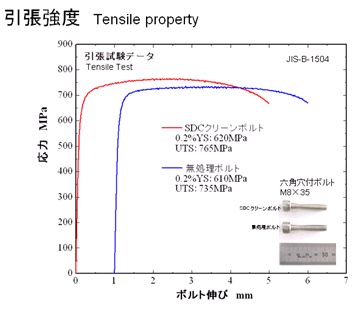
(第3図 引張試験データ)
4-4 高温時耐熱焼付き試験
潤滑剤の使用や、めっき・コーティングなどは温度が上がると揮発や変質、さらに膨張係数の差による剥離の恐れがあることから「SDCクリーンボルト」の 高温時での耐焼付き性を試験した。供試体としてM5×16の「SDCクリーンボルト」を使用し、SUS304の板に同サイズのめねじを設け、締付けトルク 10N・mで締付けた。電気炉を使用し、200℃の雰囲気で8時間放置し、その後常温に冷却後、ねじを緩めた。それを30日間(29回)行った。
その結果、焼付き現象は全く生じない事が確認でき、また試験後のねじは限界ねじゲージによるねじの精度試験にも合格した。「SDCクリーンボルト」は高温時の雰囲気に晒されても焼付きを起こさないねじであることが確認できた。
4-5 耐食性試験
「SDCプラズマ表面硬化処理」では、オーステナイト系ステンレス鋼が鋭敏化しない低温度域での処理であるが、元の耐食性を損なっていないか確認するための試験を行った。3.5%NaCl溶液にて浸漬し72時間放置、その後外観を目視した。
結果として、無処理とも発錆が認められなかった。この試験では耐食性に関しても元の母材の耐食性が保たれている事を確認した。
5.おわりに:今後の展望
ステンレス鋼製ボルト・ナットの焼付き防止対策として、潤滑剤やめっき・コーティングなどが使えない環境の配管設備は多数存在する。「SDCクリーンボ ルト」を使用することで、配管設備内部での初期締付け、メンテナンスのねじの取り外しや締付け、高温環境下に晒されたねじの取り外し時などに焼付きが発生 しないことは、安全管理・コスト管理の面から見ても重要な問題が解決される。
配管設備の中でも特にねじ締結を確実に締付けることが設備全体の維持管理・安全に直結することであり、「SDCクリーンボルト」をご使用頂くことにより品質管理の徹底を図って頂ければ幸いである。
今後も使用実績を積み重ねることによって、より一層安心してご使用頂ける製品とすることが当社の使命である。
■筆者紹介
村上 恒成(むらかみ つねなり)
株式会社田中 東京営業所

半導体製造装置内の設備の組立て時に本体のタップにキャップスクリューを締めていましたが、外すときにボルトが焼付いて取れなくなったり、本体を傷つけてしまうことがありました。高価な設備なので、何とか対策を取りたいのですが、良い製品はありますか?
(半導体製造装置 設計部 ご担当者様より)
ステンレス鋼ボルトの焼付き・かじりを防止します
ステンレス鋼ボルトは締結時に、ねじ部の膨張が大きくなり焼付きが起きやすくなります。「SDCクリーンボルト」は、「SDCプラズマ表面硬化処理」によっ て金属内部に傾斜的な硬化層が得られているため、強いトルクで締めても焼付き・かじりは発生しません。是非「SDCクリーンボルト」をお使い下さい。
食品製造設備での使用なので、潤滑剤やめっきが使用できません。洗浄のため、何度も生地(無処理)のままで締めると、ステンレス鋼ボルトが焼付いてしまいます。「SDCクリーンボルト」はねじ面に何かコーティングをしているのですか?
(食品製造設備 安全対策管理部 ご担当者様より)
潤滑剤を使用しておりません
「SDCクリーンボルト」は”無潤滑”で乾燥式の焼付防止処理です。焼付き防止として使用している「SDCプラズマ表面硬化処理」はめっき・コーティング などとは異なり、生地そのものを硬化させる処理のため、締結時に硬化層の剥離はありません。異物の混入がなく、食品関連設備でも安心してお使い頂くことが できます。
真空環境での使用のため、潤滑剤が使えません。無処理でステンレス鋼ボルトを使用しているのですが、1回締めて外すとねじ山が痛んで(荒れて)います。「SDCクリーンボルト」は繰り返し使用できるのですか?
(真空設備 品質管理部 ご担当者様より)
繰り返し使用できます
「SDCクリーンボルト」と無処理のステンレス鋼ボルト(SUS316L)で締付け後の状態の比較を行った結果「SDCクリーンボルト」は締付けた後でもねじ部の状態は締付け前の状態を保っていることを確認しています。繰り返し使用に安心してお使い下さい。
高温環境下にてステンレス鋼ボルトを使用しているのですが、潤滑剤を嫌う環境です。また、常温に戻してメンテナンスのために取り外したところ、焼付いて取れ なくなっていることがあります。設備保全、メンテナンスコスト削減のために「SDCクリーンボルト」を使用したいのですが、高温環境下でも使用できるので しょうか?
(自動車メーカー 技術部 ご担当者様より)
高温環境下でも焼付きません(推奨最高使用温度300℃程度)
一般的に潤滑剤の使用や、めっき・コーティングなどは温度が上がると揮発や変質、さらに膨張係数の差による剥離の恐れがあります。 「SDCクリーンボルト」は、200℃の高温環境に一定時間放置し、その後、常温に冷却してねじを緩める試験を行った結果、焼付き現象は全く生じないことが確認されました。 また、試験後のねじは限界ねじゲージによるねじの精度試験にも合格しています。安心して「SDCクリーンボルト」をお使い下さい。
潤滑剤を使用しないステンレス鋼ボルト・SDCクリーンボルト
潤滑剤なし、不純物なし!
「焼付防止機能付き」クリーン環境用ボルト
SDCクリーンボルト
ステンレス鋼ボルトの欠点は、締付けたときに焼付き・かじりの問題がおこることにあります。
その問題を解決するために潤滑剤やコーティングを施したりしますが、半導体製造装置に使用される真空チャンバー内部、クリーンルーム内部、食品機器及び飲 料機器内部では、潤滑剤やコーティングの剥離物質がパーティクルとなり品質に影響を及ぼしたり、食品関連機器に至っては食品衛生上品質管理が厳しく叫ばれ ているご時勢でもあります。
そこで、潤滑剤を使用しない乾燥式の焼付防止タイプのステンレス鋼ボルト、SDCクリーンボルトが新製品として販売されることとなりました。
(セミコンJAPAN2007 in 幕張メッセにてブース内展示)
・高温環境内使用
・クリーン度が必要
・潤滑油が使えない
・焼付いてしまう
↓↓↓↓SDCクリーンボルトをご使用下さい!!
サンプル【例】

表面処理
【SDCプラズマ表面硬化処理】
炭素イオンをステンレス鋼金属表面に拡散させて、表面硬度を傾斜的に向上させることにより、焼付き・かじりを防止します。
半導体向けに、真空用ガス逃げ穴加工、精密洗浄+クリーンルーム用梱包(SDCクリーンルーム梱包仕様)なども対応可能です。
SDCNEWS_Vol.15_SDCクリーンボルト
まずは弊社営業担当までお問合せ下さい。
ゆるみ止め効果のボルトについて
振動箇所に最適!!
ゆるみ止め効果絶大!!
SDCボルト【ハードロックナット仕様】
ナットのみSDC処理

弊社は1982年にハードロック工業(株)殿と業務提携を行い、ハードロックナットにSDC処理を施した『SDCボルト(ハードロックナット仕様)』 の製造・販売を行ってきました。
焼付防止・適正軸力の効果のあるSDC処理と、クサビの原理を応用した「ゆるみ止め効果」を持つハードロックナットを組み合わせることにより、外部からの衝撃や振動に対しても全く影響されることなく締結状態を維持します。
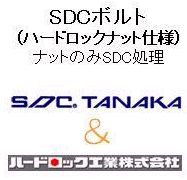
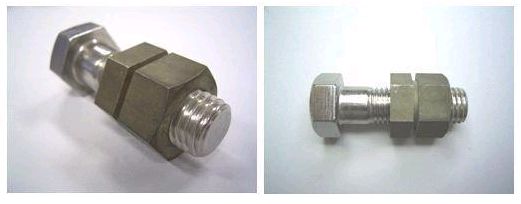
特長
●「SDC処理+ハードロックナット」を採用することにより安全性、着脱性、作業性がより確実になり、締結後のゆるみの心配がありません。
●ナットにSDC処理を施していることから、SUSボルトの弱点でもある焼付きの心配はありません。
ご利用箇所
●鉄道沿い、高速道路沿い、水管橋の配管など(車両による振動に対応)
●浄水場、配水池、ポンプ場など(設置設備などによる振動に対応)
●その他振動が発生すると考えられる箇所
SDCNEWS_Vol.14_SDC処理+ハードロックナット
チタンボルトの機械的性質&耐食性
ボルト締付けには「耐力値」が重要です。
チタンボルトの機械的性質の引張応力や耐力値を見てみましょう。
機械的性質&耐食性
チタンの使用実績
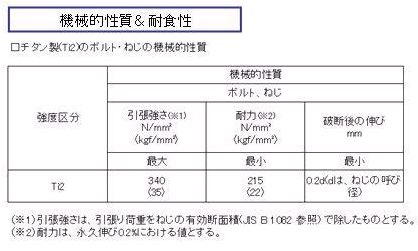
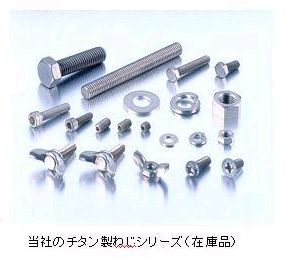
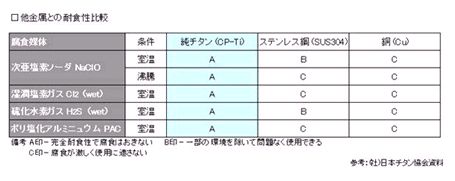
純チタン製品・在庫サイズ表
詳しい説明・表などは、下記SDCNEWSへ!!↓↓↓
SDCNEWS_Vol.23_チタンボルトの機械的性質&耐食性
ボルトの使用には、「耐力値」が重要です!
耐力値について
一般的に金属の強さを表現する方法として、引張強さなどの数値を基準にすることがありますが、その数値はあくまでも破壊する力なので、実際にはそこまで力をかけることはできません。
そこで!!
重要になってくるのが「耐力値」とよばれる数値です。(※)
金属には全て弾性があり、引張り力を加えても元に戻る性質があります。しかし、ある一定の力を加えると元に戻らなくなるポイントがあり、そこが耐力値になります。
つまり、ボルトの締付け力(軸力)というのはこの耐力値を基準に考えなくてはなりません。
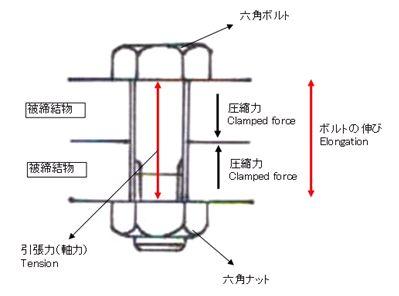
(※) ステンレス鋼は降伏点を示さないため、降伏点のかわりに耐力値で示します。これは応力(荷重)を抜いても元に戻らず0.2%の 永久伸びが生じたときの応力を試験前の材料片の断面積(mm2)で割った値です。N/mm2(kgf/mm2)
ステンレス鋼ボルトの機械的性質や有効断面積及び引張応力と耐力の実数値などの詳しい説明は、下記SDCNEWSへ!!↓↓↓
SDCNEWS_Vol.22_SUS-耐力値が重要です
異種金属接合時の絶縁ボルト=SDC防食ボルト
異種金属の接触による電池腐食防止に重要な役割を果たします
SDC防食ボルト(SUS304等)
特長
・電食防止
・良好な絶縁性
・SUS316に優る耐食性
・日水協検査合格品
・焼付防止
・適正軸力確保
・通常ボルト軸径と同サイズで作業性抜群
(スリーブをはめる手間が必要なし)
・ISO9001審査登録
使用例
■実績
全国の上下水道局、浄水場、配水池、下水処理場など数百ヶ所以上の配管設備、JRを初めとする民間企業等でもご使用頂いております。
SDCNEWS_Vol.02_SDC防食ボルト
ステンレス鋼ボルトの「焼付き」と「SDCボルト」
従来のステンレス鋼ボルトの欠点
①摩擦係数が大きい。
→ねじのはめ合いの摺動抵抗が大きくなる
②熱伝導率が小さい。(炭素鋼・合金鋼の1/3)
→ねじのはめ合いで発生した熱が発散されにくく局部的に高温になり易い
③熱膨張率が大きい。(普通鋼の約1.5倍)
→上記2点と相乗効果をきたし、ねじ山の膨張が大きくなる
これらの原因のため、ステンレス鋼ボルトはかじり・焼付きが発生しやすくなります。
上記の欠点を克服する防止策として、SDC処理が開発されました。
SDC処理は、焼付防止の効果はもとより、ねじとして一番大切なトルク係数値を安定させ、適正な軸力を与えられる処理です。
単に焼付きを防止するだけではなく、適正軸力(締り力)を保持するのがSDCボルトです。
SDCボルト(SUS304等):ステンレス鋼六角ボルトナット
特長
・焼付防止効果
・適正軸力確保
・日本水道協会検査合格品
・ISO9001審査登録
SDCNEWS_Vol.18_焼付防止&適正軸力のSDCボルト
ねじの締めすぎは危険です
ボルト/ナットは「強く締めればしっかりと確実に締まる」と考える人が多いのですが、それは間違っており、大変危険な誤解です。
ボルト・ナットの締結不良により起きる事故には、ナットを整備基準以上の強い力で締めたため、ボルトが伸びて強度が低下し、折れるというケースもあるのです。
ねじをしっかり締めるには
ねじには材質・サイズに応じて適正な締付けトルクがあり、 適正な締付けトルクで締めれば、適正な軸力が得られ、しっかり締結されます。
一方軸力(締付け力)とは、実際に締めた時、伸びたボルトが元に戻ろうとしてナットを締付ける力のことです。締付けトルクと軸力との関係は摩擦力の影響を受けるので、ねじに使用する潤滑 剤の違いにより、同じトルクを掛けてもねじにかかる軸力は変わります。
《 締付けトルクと軸力 》
締付けトルクとは、締付け方向に与える回転力のことです。(例えば1kgf/cmのトルクとは、回転軸に1cmの棒を直角につけ、先端に計りをつけて計ると1kgを指す大きさの回転力です)
潤滑剤の違いによって軸力は変わる!
ボルトM16に、締付けトルク650kg/fをかけた場合について見てみましょう。
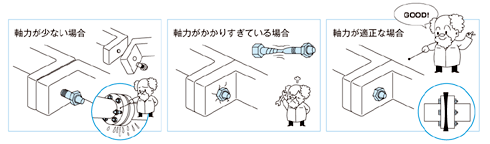
SDCボルトは、適正な締付けトルクで締めれば、適正な軸力が得られ、焼付き、かじりが起きず 安心して使用できるよう設計されています。トルク計数値は0.12~0.22と定めております。
トルク管理によって適正な軸力が得られるSDCボルトの使用をお勧めします。
ねじの性能を確かめるために
新素材の開発競争が激化する中、ねじで締結される部材もますます多様化しています。そのため、「きちんとねじが締結できるかどうか」を実証することが、非常に重要になってきています。
「SDCねじ性能試験機」によるネジ評価試験の有効性
ねじは、単体としての性能もさることながら、締結体としての性能が最も重要です。ボルトの脱落など による事故の一番の原因は、締結管理の不具合によるものです。
ステンレス鋼ボルト・ナットは焼付き、かじりが発生しやすい性質を持っています。
SDCボルトはトルク係数値を0.12~0.22に定めており、適正なトルクで締付ければ適切な軸力が得られるだけでなく、焼付き、かじりが起こらない設計になっています。